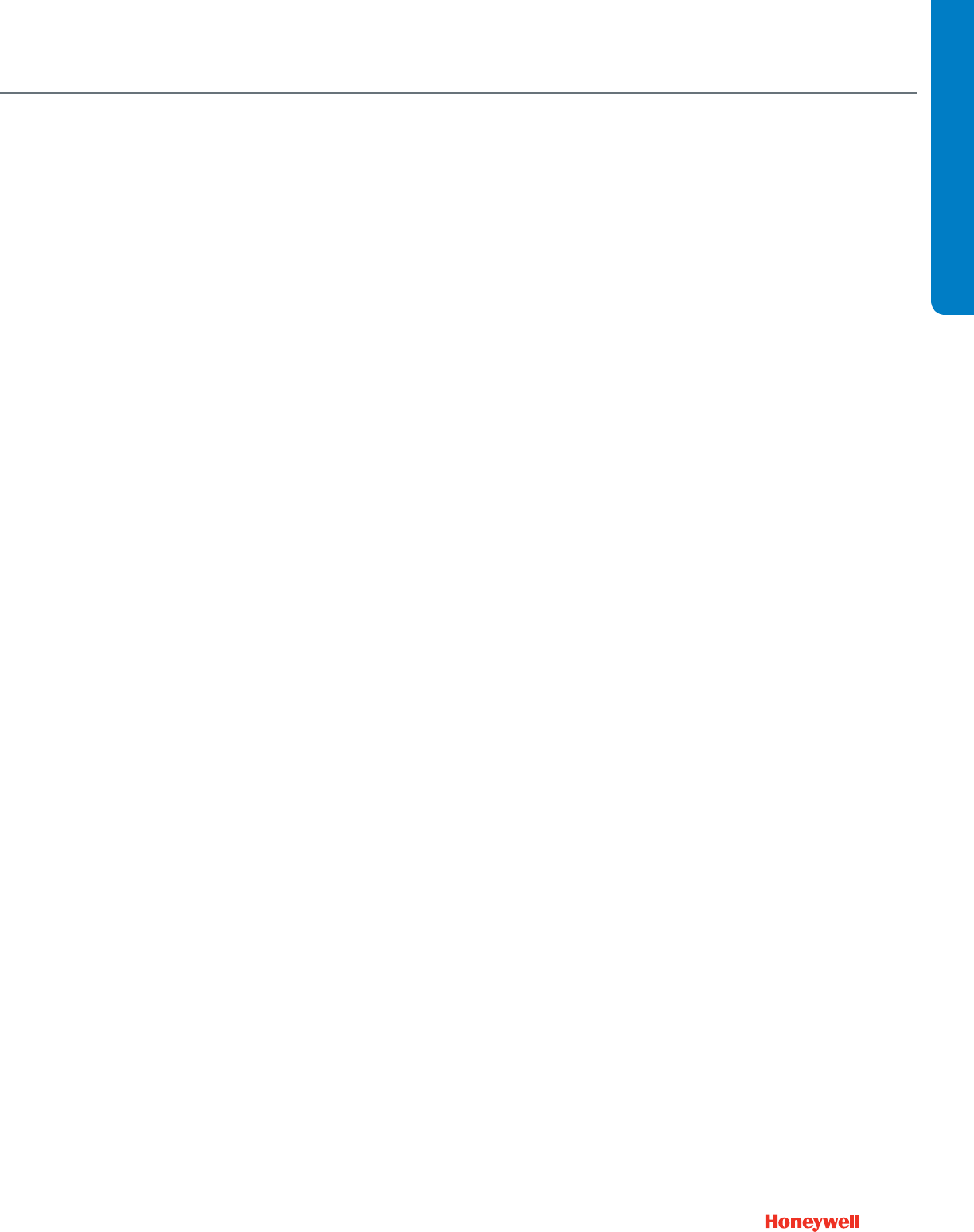
171
GUIDE SPECIFICATIONS
23 00 00 HEATING, VENTILATING, AND AIR-CONDITIONING (HVAC)
23 09 00 Instrumentation and Control for HVAC
23 09 13 Instrumentation and Control Devices for HVAC
23 09 13.33 Control Valves
Pressure-Balanced Flanged Globe Valves
Mounting
1. Flanged globe valves shall be cast iron with ANSI/ASME 125 flanges in sizes from 2 ½ up to 6 inches (DN65 to DN150), maximum
temperature 353°F (178 C).
2. Valve dimensions will conform to ANSI/ISA S75.03.
3. Cv ratings shall be a geometric progression.
4. Valves shall offer equal percentage or linear control characteristic.
5. Valves shall have stainless steel stem, plug and seats.
6. Valve stroke, sizes 2 ½ and 3 inches (DN65-80), shall be ¾ inch (20 mm) for precise control. Undercut bonnet of 1 3/8 inch (35 mm)
diameter shall allow linkage or direct-coupled actuator attachment by U-bolt, twin set screws, or mating clamp.
7. Valve stroke, sizes 4 to 6 inches (DN100-150), shall be 1 ½ inch (38 mm) for precise control. Undercut bonnet of 1 7/8 inch (48 mm)
diameter shall allow linkage or direct-coupled actuator attachment by U-bolt, twin set screws, or mating clamp.
Control
1. Actuation shall be electric or pneumatic. Actuators may be direct-coupled linear operators, or rotary actuators attached by means of a
linkage. A dual tandem linkage for rotary actuators will provide enhanced close-off ratings.
2. Electric actuators shall provide two-position, floating, or proportional control. Proportional control refers to direct acceptance of 0-10
Vdc, 2-10 Vdc or, with addition of a 500 ohm resistor, a 4-20 mA input signal. Floating control refers to direct acceptance of 24 Vac
pulse-width modulated open and close commands from a tri-state (SP3T) controller. Two-position control of non-fail safe actuators
shall be in the form of 24 Vac power controlled by SPDT switch. Two-position control of fail safe actuators shall be in the form of 24 Vac
power controlled by SPST switch.
3. Globe valves shall have minimum 50:1 rangeability with an equal percentage flow characteristic for water or linear flow characteristic for
steam or chilled water control.
Other
1. Valves shall have spring-loaded, self-adjusting, Teflon® packing.
2. All valves must be field serviceable without the need to remove the valve from the piping, in order to minimize future service costs.
3. Valves may not be installed with stems below the horizontal plane to prevent actuator damage due to stem seal leakage, or accumulation
of particulate in the stem packing.
4. Valves controlling steam should be installed with the actuator beside the valve, not above it.
5. Operating pressure of high pressure steam-rated valves shall not exceed 125 psig (860 kPa). Superheated steam must not exceed the
temperature rating of the valve.
6. A water filtration and treatment system shall be installed and operated according to the requirements of Division 23 25 13, Water
Treatment for Closed-Loop Hydronic Systems. The presence of excess rust in the system will void the manufacturer's warranty.
7. Actuated valves shall be capable of closing off against 175 psid (1200 kPa). Seat leakage when closed shall be ANSI/ASME Class IV,
0.01% maximum.
8. Differential pressure for quiet operation shall be at least 20 psid (138 kPa).
9. All valves and actuators shall be manufactured under ISO 9001 International Quality Control Standards.
10. Valves and actuators shall be as manufactured by Honeywell.
Guide Specifications
Pressure-Balanced Flanged Globe Valves