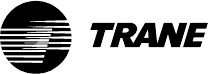
®
Glossary
58 CNT-APG002-EN
error deadband
A PID setting that defines how much the error must change before the
PID loop reacts. Used to compensate for bearings, linkages, and other
mechanical items.
gain
The primary tool for tuning PID loops, gain determines how a particular
part of the PID calculation contributes to the final output. The bigger the
gain, the more a part contributes. The proportional, integral, and deriva-
tive calculations each have an associated gain setting. Gain is defined as
the output range divided by the throttling range (multiplied by a scaling
factor for each part of the PID calculation). See also throttling range.
hysteresis
The programming of equipment to react in a different way depending on
whether the control value is increasing or decreasing (Figure 31 on
page 43 illustrates hysteresis).
integral control
Control action based on the sum of past errors. Used to maintain an out-
put when the error is zero. See also integral windup, error. Also called
reset control, automatic reset.
integral windup
A condition that can occur when the result of the integral calculation
becomes too great for the system to change direction. This is typically
caused when the system does not have the power to reach setpoint. Trane
uses the velocity model to minimize the problem of integral windup.
See also integral control, velocity model.
measured variable
Typically, a value read by a sensor, such as space temperature, discharge-
air temperature, or duct static pressure. The measured variable is sub-
tracted from the setpoint to determine the error. See also error.
Also called process variable.
overshoot
When a controller responds too aggressively to error, it can push the con-
trolled variable past the setpoint. The overshoot is the amount by which
the system passes the setpoint.
PID loop
See proportional, integral, derivative (PID) loop.
process variable
See measured variable.